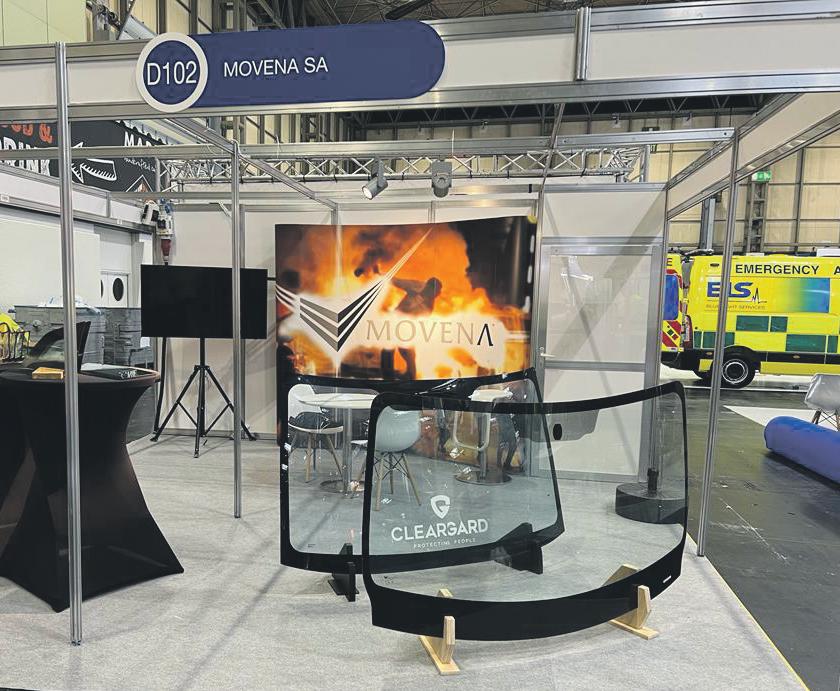
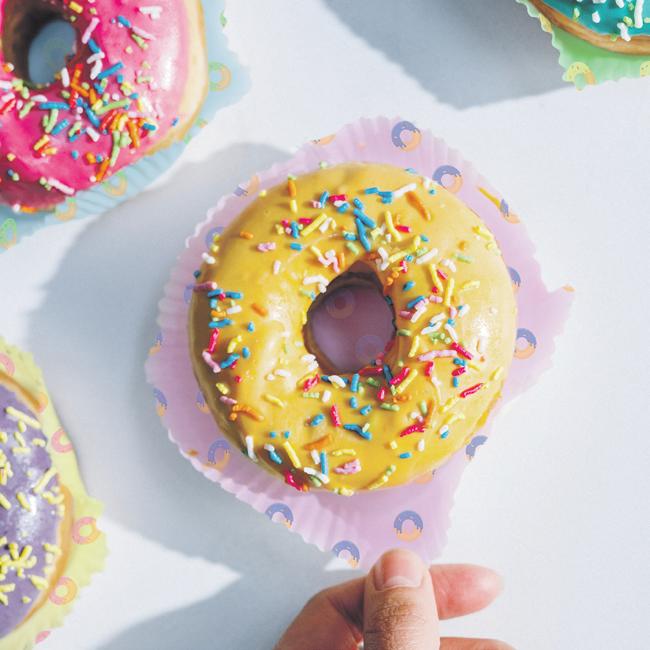

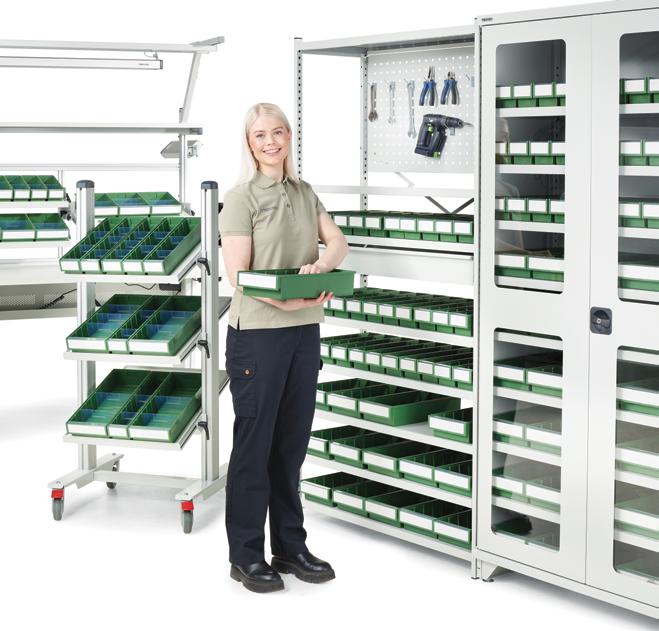
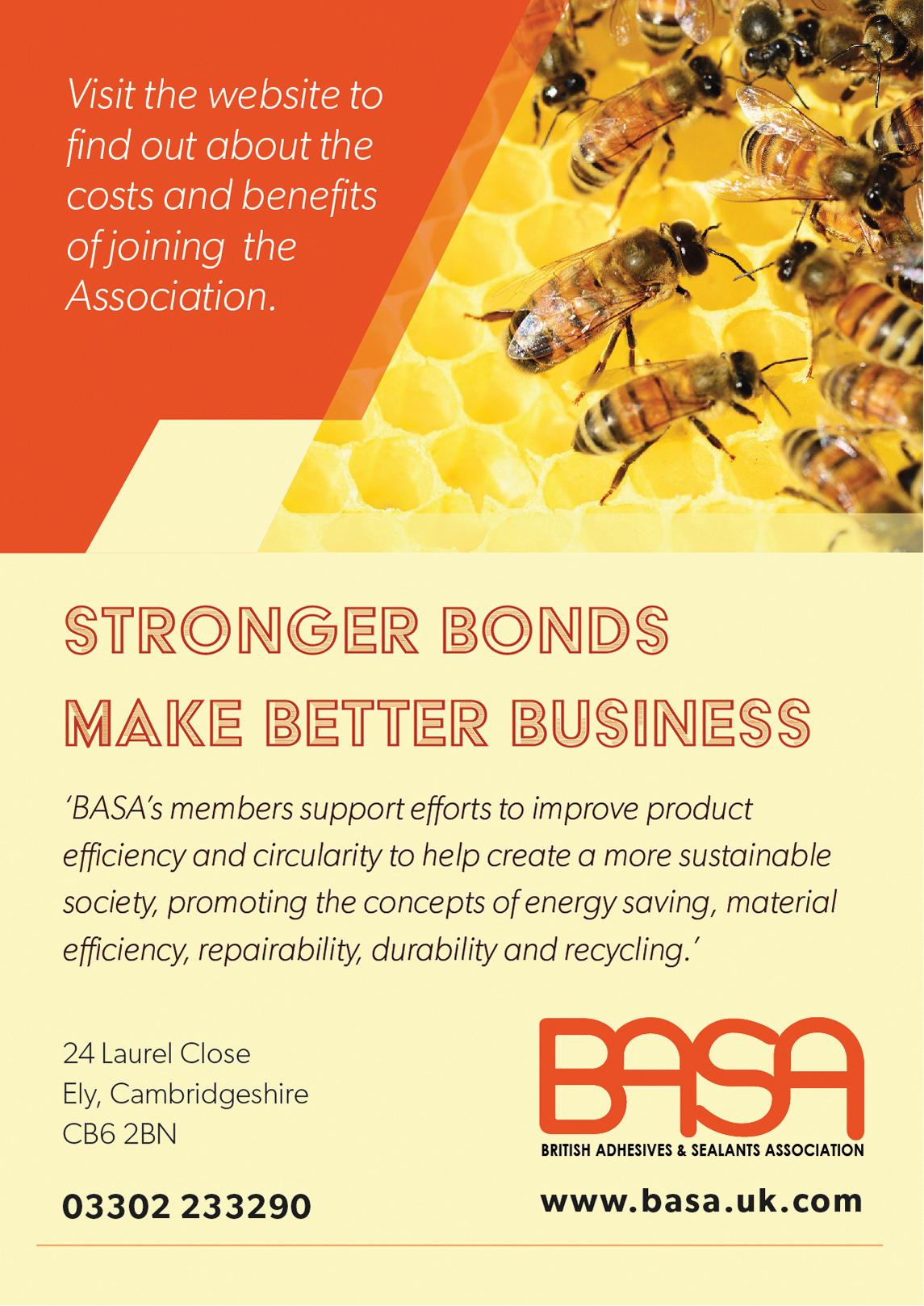
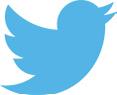
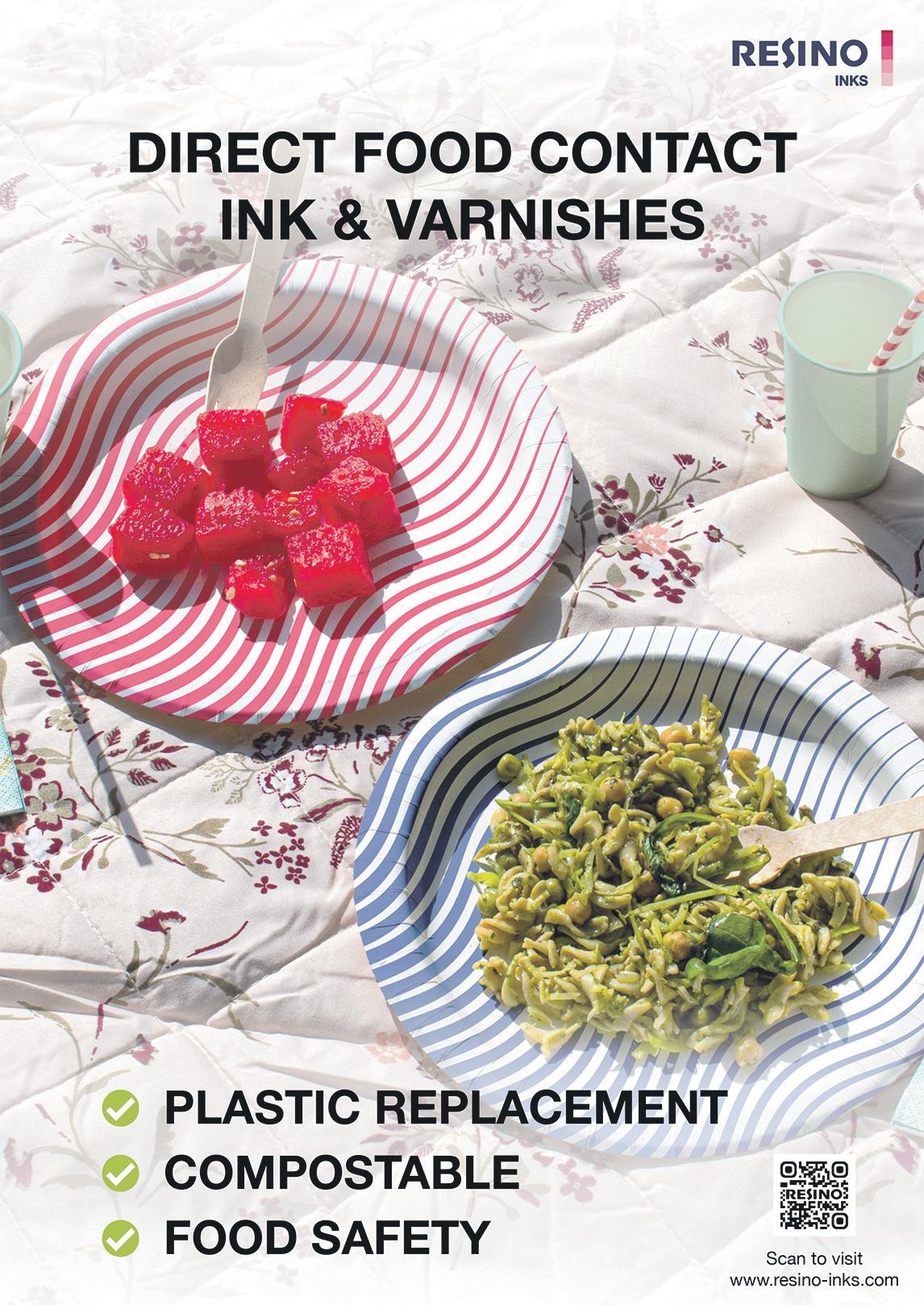
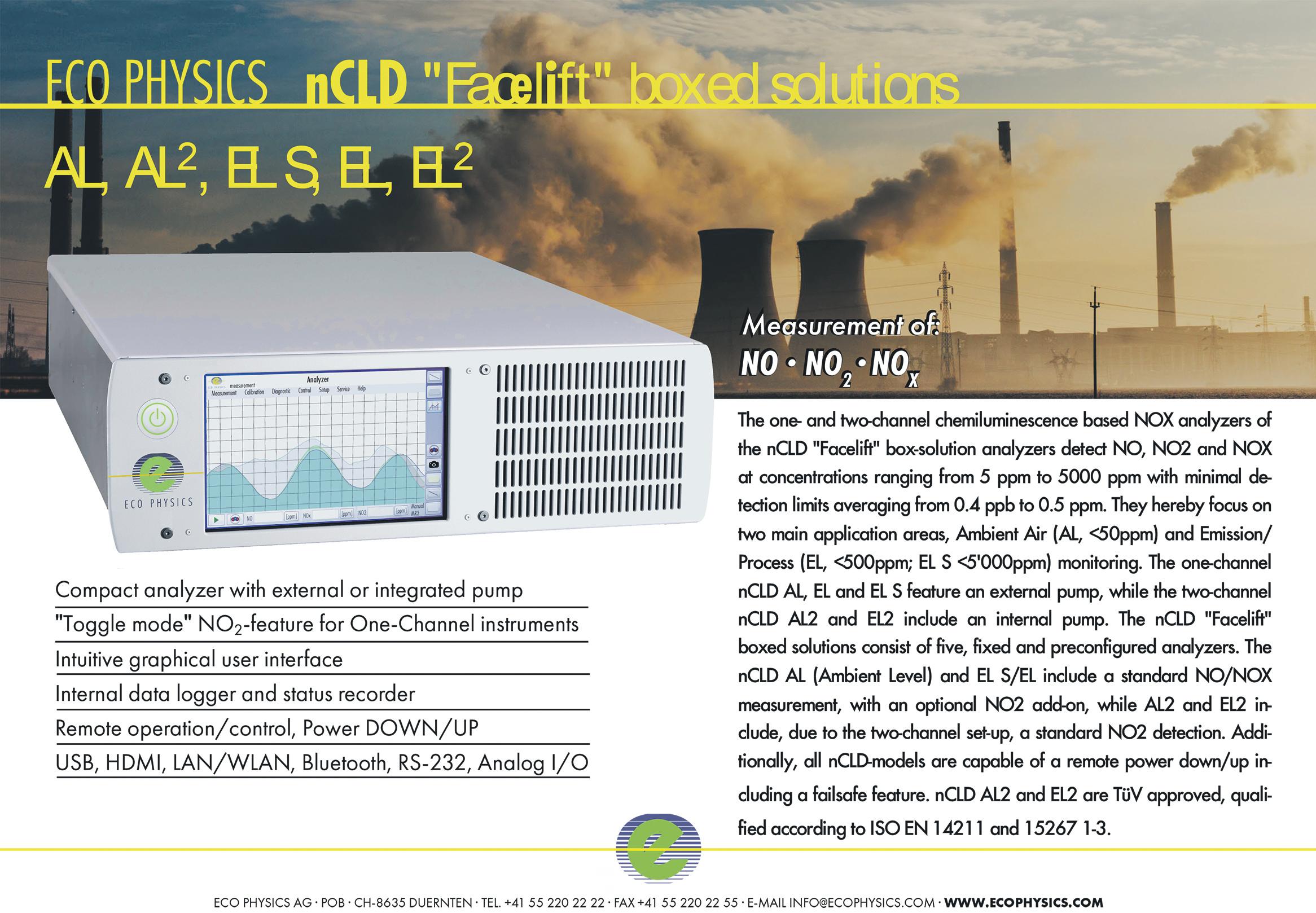
Transform redundant end-of-aisle racking space into working space with Modulean®
Rack End Boards, from visual management solutions specialist Beaverswood®
Ensuring compliance with 5S lean processes, these eye-catching shadow boards make use of otherwise ‘redundant’ space at the end of aisle racking systems. They offer an effective, easy-to-use solution for the storage and access of equipment, and are supplied with products on display. Additionally, these standardised boards remove the requirement for installing costly custom-made shadow boards.
Measuring 2,000mm high x 900mm wide to fit standard racking systems, the boards are manufactured from tough,
This year, European Springs & Pressings have been reaping the rewards of working collaboratively with their sister companies. Making their mutual platform of products and services more accessible enables them to deliver a wider range of manufacturing capability and products to their customers than ever before.
Working more closely with our UK manufacturing partners Metrol Springs and Lesjöfors Heavy Springs UK has brought significant benefits for the respective companies, as well as allowing the group to offer an unrivalled portfolio of springs, stampings and industrial hardware.
Shared attendance at exhibitions, pooling experience at cross-company strategy meetings and developing a mutual knowledge of each other’s products and specialisms has broadened the shared capability they can offer and increased the company’s sales reach considerably.
This support brings tangible benefits to clients as well. European Springs’ commitment to providing the coiling and pressing expertise customer’s need to find custommade solutions for their manufacturing processes remains unchanged, with the added assurance that when they claim to have the required capability in the UK to design and produce the optimal component at the most competitive price, they make good on that promise.
This culture of collaboration has been fostered by their parent company, Lesjöfors Springs & Pressings. Although not a household name in the UK, since its conception 150 years ago Lesjöfors has patiently and practically built from its manufacturing base by acquiring a broad network of companies with specialist capabilities and strengths.
Lesjöfors is now the biggest spring manufacturer in the Nordic region, the third largest in Europe, and has a strong and growing presence in the US and Asia. Lesjöfors’ culture of supporting innovation, and developing capability is why European Springs & Pressings Ltd. joined the group in 2007.
Their dedication to investment, both in people and technology, mirrors ESP’s, and has allowed them to develop as a business, as well as recruit and retain the talent, and acquire the machinery required to continually provide the high quality manufacturing that client’s demand.
The culture of collaboration developed within European Springs’ UK manufacturing family, alongside the marketleading portfolio of products and services across the Lesjöfors group, means that customers can continue to rely on the ESP promise - to provide innovative design solutions, reliable service and custom-made, quality components.
If you would like to find out more information on the company, please see the details below.
T +44 (0) 208 663 1800 www.europeansprings.com
scratch resistant Foamex and come in seven designs:
t Cleaning Board - featuring a mop, brush, and bucket
t First Aid Board - consisting of a wall-bracketed first aid kit
t Fire Safety Board - with fire extinguisher and fire blanket
t Racksack® Board - for the improved segregation of packaging waste materials
t Sanitising Board - including wall mounted soap dispenser
t Rack Assessment Board – including racking selfassessment chart
t White Board - with a dry wipe write-on surface
Each board comes with single or double aisle markers, plus a weight load notice sign - all supplied on one costeffective board.
Available from £172 - £399 depending on specification.
For more information, visit www.beaverswood.co.uk
OLocated in Fox Creek, Alberta, Canada - Kaybob covers an area of 330,000 acres, equivalent to 4/5 times the size of London and is estimated to produce 22,000 barrels of natural gas per day.
Almost half-way into the contract, Oliver has supplied a significant number of Instrument Manifolds, and Reduced and Full-Bore Double Block & Bleed valves from our sister company Twinsafe, with injection and sampling probes, in orders placed so far worth over £500,000. Oliver engineers carried out strength calculations that was were needed to gain approval and to obtain Canadian Registration Numbers (CRN), which is
a legal requirement for pressure rated products to be installed and operational in Canada.
An exciting project for Oliver’s to be a part of explains Martin Orme, Key Account Sales Engineer. “We have worked with distributors and energy contractors in the U.S and North America for such a long time that our experience of designing and developing valves for specific applications with clients is largely the reasons why Oliver’s are selected for major projects such as this.”
Valve safety, performance and manufacturing quality are the cornerstones of Oliver’s success and their strong customer relationships are what set them apart from other suppliers. Another unique strength is their dedicated Research &
Development facility in Knutsford, England.
Martin continues, “Obtaining relevant documentation and registrations like CRNs can be an arduous task, but by having a dedicated research, development and testing centre, we’re able to meet the most stringent of end-user specifications such as we have done on this scope of work.”
Oliver Valves and its sister company Twinsafe, who specialise in pipeline valves, work with clients around the globe on oil, gas and hydrogen projects to provide worldclass valve solutions that include Zero-rate A valves for hydrogen applications.
Visit their website for more details at: valves.co.uk
Our Research and Development Centre based in the UK is world-leading in the technology to seal, test and innovate valves for Hydrogen, Carbon Capture and Subsea applications.
One huge part of our R&D operation is automation. As well as giving us the ability and capacity to test multiple projects simultaneously, it also allows us to replicate demanding environments to ensure that valves are qualified to meet the most robust testing criteria in the industry.
To rapidly collect, process, and analyse significant amounts of data from multiple sources, you need a powerful processing capacity with precision and accuracy. Our data processing network is custom-built in-house and is tailored to our valve designs, ensuring that we maximise the performance and safety of each valve we manufacture.
We have a strong mix of engineering skills within R&D which are resulting in amazing achievements, such as designing the first ball valve to be qualified by a third-party for hydrogen application. Our engineers are long-serving and have decades of experience and are instrumental in passing on their knowledge and expertise to apprentices joining the business. This invaluable work is reciprocated by their enthusiasm for new engineering technology that’s helping drive and shape our future development projects such as automation.
Each year Oliver places significant investment in its people, processes and systems, and this was certainly evident in 2022 with the installation of new testing rigs in two factories that exceeded the cost of £1m. Yet again, an example of the confidence we have in the future of valves, especially at a time of very difficult challenges and uncertainty that surrounds the UK economy, and with the ongoing energy and cost of living crises. The future looks very positive and we’re well-placed in leading valve development within the energy industry.
For more information, see below.
www.valves.co.uk
Veolia Water Technologies UK (VWT UK) recently supplied a water treatment solution to optimise the operational processes at a large-scale gin distillery. By adding its Hydrex™ 4301 water treatment chemical via a single dosing pump, VWT UK successfully removed excessive levels of residual free chlorine from the feedwater to improve the efficiency of the water conditioning units and prevent damage to the water softeners.
One of the oldest distilleries in the world, producing a significant percentage of the UK’s gin, the company uses a set of water conditioning units to process approximately 30m3/hr of raw water.
However, since moving location, the distillery suffered from an uncontrolled deterioration of the ion exchange resin beds inside these units. While this issue did not affect product quality from the site, it resulted in increased CAPEX to maintain the required levels of gin production. This was due to excessive levels of residual free chlorine, approximately 0.89 mg/l, in the facility’s feedwater.
Therefore, the distillery decided to work with a water treatment specialist that could help to reduce the presence of residual free chlorine in the feedwater to approximately 0.2 mg/l, a level that would not damage the distillery’s water softeners. It was also crucial that the solution was installed efficiently to resolve the issues as quickly as possible.
Following a competitive bid, the company selected water treatment specialist VWT UK. VWT UK had previously carried out periodic servicing of the distillery’s water softeners and reverse osmosis (RO) systems, so the two companies had a good rapport.
To effectively treat the residual free chlorine for removal from the facility’s feedwater, VWT UK supplied its Hydrex™ 4301 – a water treatment chemical that is specifically formulated for RO systems with polyamide membranes that can be affected by chlorine.
As it was vital that the issue could be resolved with minimal operator input, VWT UK installed a single dosing pump with flexible dosing pipework and an intermediate bulk container (IBC) bundstand. The dosing pump was then connected via a 110v lead and socket to transmit a signal to stop and start dosing depending upon whether the water feed pump was active. This ensured that the Hydrex™ 4301 chemical was only dosed when required.
Thanks to the water treatment solution, the distillery has now been able to reduce the level of residual free chlorine in its feedwater to <0.2 mg/l and prolong the life of the components in the water softeners. This eliminated the need to bring in demineralised water with the use of road tankers, a process that had been required when the resin beds had failed previously.
The company has also been able to accurately baseline its facility output and plan its day-to-day operations more effectively, resulting in reduced unplanned spend and CAPEX while maintaining the same levels of gin production.
“I was delighted to provide a simple and effective solution to one of my local businesses. The dosing system is still going strong after being in operation for over 12 months. The site is very happy with the extremely low usage of Hydrex™ 4301, which is even lower than originally estimated,” commented Brian Jones, Business Development Manager (North and West) at Veolia Water Technologies UK.
For more information on Veolia Water Technologies UK and its range of solutions, including its range of Hydrex™ water treatment chemicals, visit: www.veoliawatertechnologies.co.uk.
Foremost
Electronics the engineering-led Essex based importer and specialist distributor of electromechanical components, is a key source of supply for machine builders looking for rugged and reliable enclosures, human machine interfaces (HMI) and secure cable entry systems.
Channel partners for the German manufacturer nVent Schroff, Foremost can supply their range of cabinets,
Blackman & White is the UK’s only manufacturer of flatbed cutting systems, and all machines are designed and manufactured at its Maldon, Essex
factory. Founded in 1964 by engineers Jack Blackman and Les White, the machines are renowned for their robust build quality, and quickly delivering a return on investment.
“Opening our demonstrations and training centre in early 2021 was a real game-changer,” comments commercial sales manager, Matthew Tillett. “The quality of service we provide customers has increased, and offering over three B&W demonstration machines for tests allows them to leave with all questions answered.”
Whilst kit cutting is one of its strongest sectors, B&W
has increasingly found companies diversifying into others also. Tillett believes this is down to the current climate, where sourcing products from independent manufacturers is preferred.
“Our diverse range covers a wide array of materials, including glass fibre, carbon fibre, Kevlar, and thermoplastics. Having our 200W laser mounted directly next to two interchangeable tool slots provides a solid platform to cover all materials and applications.”
Why do customers specify a new flatbed cutting system?
Is it an increase in volumes, a need for faster production throughput, or quality requirements?
“All of the above, but every customer has their reason for purchasing our systems,” states Tillett. “The biggest trend is the support from the manufacturing community in seeing the value in an independent manufacturer who can truly design and build something bespoke - the bespoke touch is always built into our systems.”
“Progressive Technology Group selected Blackman & White to manufacturer a new cutting system in line with its new cutting-edge facility,” Tillett continues. “Operations director, Daniel Smith approached us to supply his new facility with a material cutting system.”
“During demonstrations, the Genesis V proved to be accurate, easy to operate, and importantly, quick. The Lite digitising system was crucial in Progressive Technology’s choice, as it translates templates and file formats quickly, reducing any bottlenecks in the material-cutting process. As our business is UK-based, we offered quick turnaround times for routine servicing and breakdown, which is critical to keeping their business operational.”
Tillett also tells us that, “During COVID-19 B&W adapted quickly, continually modifying our machines, plus being honest about when we could deliver. We didn’t experience much downtime, but the lack of external visits and networking allowed us to finalise internal development.”
“The key development is our new drive system, which pushes the Genesis V system above comparable market models regarding cutting time and methods. Our future is about the flexibility of tooling and machine specifications, with rapid innovations in materials creating a push for new tooling additions and chassis sizes.”
B&W are relocating to a larger facility to house all manufacturing, service, support, development, and sales. They acknowledge that without its clients, the company wouldn’t be in this position to grow and continue supporting them.
“Blackman & White has been a family-owned, profitable company for over 50 years,” Tillett concludes. “We pride ourselves on customer support and value for money with manufacture and design completed in-house. With a proud heritage of customers and continual improvement, our systems are ‘class leading’ in the industry.”
For more information:
T +44 (0)1621 843 404
www.blackmanandwhite.com
Assessing the life cycle of an industrial or commercial metal roof before PV panel installation
75% of the carpet and textile flooring sector engages with Carpet Recycling UK
Carpet Recycling UK is an independent not for profit membership association dedicated to helping the UK carpet and textile flooring sector become more sustainable. Working with the whole supply chain, it helps foster strategic collaborations and networking to develop viable solutions for carpet and other textile flooring waste such as carpet tiles, rugs and underlay.
Carpet Recycling UK’s membership now includes around 75% of the manufacturers placing product onto the UK market who are taking voluntary producer responsibility ahead of any policy changes. Core Members are Balsan, Betap, Brintons, Condor
Group, Cormar, ege, Furlong Flooring, Gradus, Headlam Group, IVC Commercial, Likewise Floors, Milliken, Modulyss, Rawson Carpet Solutions, Shaw, Tarkett and Victoria Group.
Through Carpet Recycling UK, the sector is becoming more aware of the Circular Economy and companies are helping their clients with sustainable product ranges, as well as with opportunities for segregating waste streams into reuse, recycling and treatment processes.
Find out more about joining.
www.carpetrecyclinguk.com
T
Here at Industry Update, we would like to congratulate Movena on being our Company of the Month for specialist automotive safety glazing.
Movena is a leading European manufacturer vehicle windscreen: side and rear safety glazing for the emergency services: police, fire and ambulance. The high-impact resistance laminated glass and polycarbonate glazing protects emergency workers from potentially fatal attacks from pick axes, hammers to stones, used under increasing urban unrest. Tested to the highest UK safety standards: EN 356 and European Certification R43; the thin yet robust glazing can sustain multiple attacks from protestors or rioters.
This Belgium-based company started trading in 2002, where it successfully supplied the French fire engines with protective glass and has grown exponentially to now supplying an impressive 10,000 vehicles across the French emergency services market. We caught up with Managing Director Phillippe Van Damme to find out more,
“Our laminated glass is perfect for everyday police vehicles, who may experience the occasional attack from members of the public. It is a thin glass, similar in thickness to existing windscreen glass, but with added protection for the occupants. For police riot vans, that deal with multiple potential attacks, we would recommend the polycarbonate glazing. This offers protection, under sustained attacks, allowing police officers to remain protected at all times.
The impact performance glass is guaranteed for the lifetime of the particular vehicle, for peace of mind.
In the UK, we have supplied anti-bandit glass to 100% of Volvo fire engines and many police vehicles in Leeds and Newcastle.
Each piece of glass is tailor-made to the vehicle’s exact specifications. We are currently supplying mainly to France and the UK, with other orders in Italy, Belgium and Scandinavian countries. We are aiming to expand into Germany and The Netherlands in the future, with increasing European demand for protected emergency services vehicles.”
Movena can supply directly to emergency service departments, car converters who convert vehicles to emergency service vehicles and car production teams.
The Movena team attended The Emergency Services Show at the NEC in Birmingham 2022 and was inundated with requests for lighter glass orders, as Phillippe explains,
“In Europe, any vehicle over 3.5 tonnes needs a specific driving licence, which can cause difficulties for ambulance drivers. Medical equipment used in ambulances has
increased in weight, so coachbuilders are looking for innovative solutions to keep the total weight under 3.5 tonnes. We were approached and asked if we could manufacture lighter windscreen glass for ambulances, to compensate for the heavier equipment weights. We have successfully been testing our lighter glass designs and have noticed that this will save ambulance vehicles up to 20kgs in weight.
We will be back at this year’s Emergency Services Show, to showcase the whole range of our lighter vehicle glass together with our high protection anti-bandit glass against urban violence.”
Movena has been part of the Fahrner Group since 2021: this acquisition will give more opportunities to both companies and help them to improve their sales development across Europe.
The leading automotive safety glazing manufacturer is hugely committed to sustainable development and is trailblazing by only using 100% recyclable laminated glass; perfect for companies looking for greener manufacturing investment.
The Movena will be back at The Emergency Services Show at the NEC from 19- 20 September 2023.
To find out more about Movena’s range of products, see the details below:
T + 32 (0) 10238580 info@movena.com
www.movena.com
At this year’s PPMA show Soken Engineering, a recently acquired subsidiary of Jenton International, will launch an all-inclusive range of heat sealing packing systems for ‘on the go’ food businesses wanting to improve presentation, product lifespan and handle a varied range of lunch products on a single system!
Deli’s, garden centre cafes, hospitals and garage forecourts that hand-pack lunch items in takeaway cartons/boxes with press-on lids will compromise product presentation and lifespan due to air leaks which fast-track spoiling. As the UK’s demand for lunch products continues to broaden, Soken has responded with a 3-in-1 Heat-Sealing System which perfectly seals packs of sandwiches, wraps and salads with only the need for a tool change. Now artisan businesses only need to invest in a single system to improve pack presentation, hygiene and preserve lunchtime foods by up-to three days, putting a stop to food waste and resulting loss of profit which is entirely preventable.
The 3-in-1 Soken range includes level 1 machines ideal for small cafes which want to seal a single pack at a time, level 2 machines – which seal up to 4 packs at the same time – ideal for caterers supplying mobile vans and local shops, as well as level 3 intermediate automated systems – which can output up to 48 packs per minute – perfect for medium sized businesses such as airline caterers or large garden centre chains.
All Soken equipment is manufactured in the UK and backed by a two-year return-to-base warranty. As all tooling and parts are designed and manufactured in-house, spares can be provided within very short time scales. It also means that if a caterer has any unusual packaging requirements bespoke tooling can be developed as required. In addition, Soken can supply all necessary consumables such as sandwich packs, ready meal trays with lidding film and salad boxes. Plans are in the pipeline to develop packaging options which are plastic free.
Stephen Hawes, Soken Engineering sales manager said: “If sandwich boxes and salad packs are not sealed properly the shelf life of the food is compromised leading to waste and reduced profits. Our versatile easy to operate 3-in-1 ‘fresher for longer’ packaging systems give catering outlets the ability to sell a wide range of foods in tamper evident heat sealed packaging which extends shelflife considerably. As a business we are always striving towards net zero so helping reduce food waste is a key priority.”
For further information please visit: www.sokenengineering.com
For over 25 years Allpack has been providing its ‘Gold Standard Service’ to warehousing & logistics customers, with the combination of high-quality products, and first-in-class service. Customers of Allpack can rest assured knowing they are using industry recognised products, designed specifically for stable loads on each vehicle they despatch.
Allpack employ unique manufacturing capabilities that offer unrivalled levels of precision over a diverse range of products. With a capacity of over 300,000 tonnes of film per annum, 600 million square meters of tape and 1,000,000 kilometres of strapping, coupled with
our highly efficient corrugated conversion machinery, producing millions of quality printed and plain cases, boxes and fittings, all ready for next day dispatch.
Our industry accepted high-clarity Vortex™ Cast film product has been specifically designed to meet the demands of the warehouse and logistic sectors, offering a consistent yield and maximum stability for each palletised load, with a silent unwind on application for optimum user-friendly wrapping.
Many of Allpack plastic products are manufactured from 30% recycled content and are 100% recyclable
making them Plastic Tax Compliant, which is better for you, your customers, and the environment.
Contact Allpack today for a free trial of Vortex™ film at your site: 01543 396 888
Through several years Resino Inks has provided customers with a safe and healthy line of printing ink for direct food contact. Through different printing principles, Resino can meet most demands in the area of food packaging.
Due to the continued focus on replacing plastic coated paper and board Resino has developed two types of varnishes for paper and board packaging offering similar protective functions as plastic thus more environmentally friendly. Varnishes that can replace plastic coating and inks for direct food contact are important milestones for Resino and is part of the contribution from our company to the circular economy and a more sustainable future.
High safety standards for food contact materials
As a supplier of ink solutions for food packaging printers, Resino is exposed to many different requirements for the printing ink. Some customers use Resino’s printing ink for an informative purpose and other customers may use it for a decorative purpose, but they all must comply with same high safety standards.
Food packaging is one of the most regulated areas for ink and packaging manufacturers – and rightfully so. The packaging can come into direct and indirect contact with food, which is why Resino strive to offer products that continuously meet or exceed the market demands.
Resino provide their customers with a safe line of regulatory compliant inks for printing applications that involve both direct and indirect food contact, in compliance with the American Food and Drug Administration (FDA), Swiss ordinance and the European Commission (EC).
“The varnishes and inks support our customers’ goal to convert from plastic to paper and board products that comply with the EU Directive,” Chief Commercial Officer Niels Nielsen says.
Replacing plastic coating with biodegradable varnish
Switching from plastic to paper and board, the so-called paperization, cause several difficulties regarding protecting food packaging and its content. Plastic is a great barrier, protecting food and prolonging the shelf-life of the food. At the same time, plastic is only rarely attacked by the food content, and plastic can act as a barrier allowing printing on the outside safely.
Therefore, eliminating plastic calls for a sustainable alternative to take on this protective function. Resino has developed the varnishes REVALUX 164 and REVALUX 156 which can replace the plastic coating –both on disposable tableware and food packaging.
With the increased focus on reducing plastic consumption due to environmental concerns, there is a great need in the market to reduce or eliminate plastic-coated food packaging and PE laminated wrapping paper.
Furthermore, the legislation has come into force within the EU, which bans the use of plastic for disposable tableware (European Union’s Single-Use Plastics Directive).
Resino has worked in close cooperation with customers to find solutions and developed more sustainable solutions based on varnishes, on acrylic binders as well as natural materials, which can replace the plastic coating.
1. Varnishes for direct food contact
The REVALUX 164 varnishes are based on natural materials and thereby presents an important milestone for Resino, as these varnishes are both
biodegradable and complaint with the EU Single Use Plastics Directive.
Products we offer:
t Varnishes replacing PE coated/laminated paper & board
t Varnishes which are Single Use Plastics Directive compliant
t Varnishes designed for direct food contact
The REVALUX 156 varnishes are based on clean chemical materials which are compliant with direct food contact regulations. These varnishes can be formulated to provide a larger diversity of performance and most importantly, higher resistance properties.
As these are chemically modifies products, they are not in compliance with the EU Single Use Plastics Directive.
t Varnishes replacing PE coated/laminated paper & board
t Varnishes designed for direct food contact
t Heat-seal varnishes
2. Printing inks for direct food contact
Resino offers inks suitable for printing on materials, where the print is directly exposed to food.
Resino’s REVALUX 156-3 series is a water-based printing ink varnish specially developed to be used for foodstuff applications on coated and uncoated carton/paper as well as most packaging films.
These inks are based on clean chemical materials which are compliant with direct food contact regulations.
These inks can meet traditional end use resistance properties, however, the pigments suitable for these applications results have limited color shade availability. If a “normal” range of color shades is required, another method may be necessary.
As the EU Single Use Plastics Directive only apply to Varnishes, not to inks, it is still possible to meet the SUPD compliance when printing with REVALUX 156-3 inks. Inks designed for direct food contact.
Based on various tests the inks described above can be used for long term contact with all types of foodstuffs for up to 40°C – as well as 70°C for 2 hours or 100°C for 15 minutes.
This allows the inks to be used on the inside of vegetable packages and on paper plates/cups and many other materials intended for direct contact with food.
Compliance
The ingredients used are suitable for direct food contact according to FDA§ 175.300 & Food contact: Regulation (EC) 1935/2004 and products tested complies with the requirements in Commission Regulation (EU) No. 10/2011 with amendments up to an including Commission Regulation (EU) 2019/1338 on plastic materials and articles intended to encounter food. Manufacturing follows Good Manufacturing Practice according to regulation (EC) 2023/2006, EuPiA, ISO 9001 and ISO 22000.
Resino work with independent institutes accredited for food packing approvals, such as Fraunhofer, Eurofins and J.S.Hamilton.
They act as a third party, investigating and validating Resino’s recipes for printing inks & varnishes, designed for print on food contact material.
The quality of the products and the approval of the types of ink & varnish for printing on food contact materials apply to most markets across national borders, however, it is always necessary to enquire about compliance with local regulations.
Our approach to direct food contact ink Inks & Coatings must be designed so they don’t damage the food.
When developing ink for direct food contact, four aspects need to be considered.
1. Food safety
2. Colour
3. Odor
4. Taste
They require a close cooperation between Raw material suppliers, Ink & substrate suppliers, printers and packaging supplier.
Ingredients
We select ingredients based on specific criteria to ensure that the inks and varnishes are as safe as possible. This includes:
EU:
To a large extent we select e-numbers or natural ingredients
t (EC) No. 1935/2004 (Direct food contact)
t (EC) No. 2023/2006 (Good manufacturing practice)
t (EU) No. 10/2011 up to 2020/1245 – Plastics
t REACH
t Packaging directive 94/62
t BfR XIV
t BfR XXXVI
t Swiss ordinance Annex 10 Edition 2.1
USA:
t 175.105 (adhesives)
t 176.170 & 176.180 & 176.200 & 176.210 (paper & Board)
t 175.300 (varnishes & Coatings)
t Proposition 65
Regulatory
We highly prioritize that the end product is regulatory compliant.
Regulatory compliance is highly dependent on:
The type of food the print will be exposed to.
t Meat t Wet
t Fatty
Other Regulatory requirements
Biodegradability / Compostability
Properties
t What is the substrate?
t Resistance properties required
t Migration / protection
t Adapted to processing
Applications
It varies which applications the inks and varnishes are developed for.
Type of food
t Dry solid
t Wet
t Fatty
t Aggressive
How is the packaging handled?
t Frozen / Cool / Hot / Oven / Micro wave
t Boiling / Sterilization
How long is the normal & extreme exposure?
t Minutes / Days / Weeks / Years
Products we offer:
t Varnishes replacing PE coated/laminated paper & board
t Varnishes which are Single Use Plastics Directive compliant
t Varnishes designed for direct food contact
t Inks designed for direct food contact
At Resino we constantly consider ways of integrating sustainability in our product development both in the form of renewable resources and biodegradability.
Food packaging design is a complicated process involving a joint effort between Brand owner, packaging printer, substrate supplier & ink supplier. We at Resino welcome your challenges.
Learn more at www.resino-ink.com or contact us for a personal dialogue.
Made from the long-lasting, innovative Sorona® performance fabric and CORDURA® for long-lasting comfort, functionality and sustainability.
It’s the innovative design and sustainable fabric technology in the newest Work Trousers for men and women from Snickers Workwear that really set them apart from other brands.
Delivering comfort and safety features when
launched new fire safe single source wall solution for all applications
Paroc Panel System in collaboration with BTS Facades & Fabrications, has launched Vantage® PPS – a fully certified single source full wall system –an all-in-one solution, which facilitates installation twice as fast as a comparable built-up system.
The Vantage® PPS is a class-leading noncombustible (Euroclass A2-s1,d0) sandwich panel with a structural non-combustible (Euroclass A1) stone wool core, combined with the CWCT tested Vantage® SF Rainscreen front face, tested to the tested to the latest BS84142:2020 standard.
Vantage® PPS system offers a number of benefits: its long-spanning capabilities reduces the need for secondary galvanised steel purlins for significantly faster construction times, reduced material use and potential cost savings. It also offers reduced cold bridging, excellent acoustics and, with panels from 80mm to 300m, a wide choice of thermal insulation options and U Values are available.
Specifically, the collaboration brings the air and water-tight structural support base of Paroc Panel System panels, manufactured using AST® Technology to ensure their high tensile strength, reliable longevity, and fire resistance to the BTS Vantage® SF Rainscreen range, itself CWCT tested and provides the ultimate design flexibility.
The Vantage® PPS system is ideal for a wide range of construction applications, including data centres, retail developments, leisure, and other commercial buildings where a fast, fire-safe, water-tight solution is required to be installed.
For details about the Vantage® PPS system panel visit https://www.parocpanels.com/ en-gb/news/2020/vantage-pps
or contact: Paul Kinsey, UK Representative T +44 (0)7876 563 175
they’re needed most, these slim-fit Trousers are Class 1 and Class 2 certified and made from innovative Sorona® sustainable performance fibre.
They also come with the patented KneeGuard® system and CORDURA® reinforcement in the knees and pockets.
Sorona® delivers both environmental benefits and long-lasting performance. This recyclable, bio-based fibre offers exceptional softness and stretchability for maximum comfort as well as excellent durability
to help extend the lifetime of a garment. It’s also quick-drying, breathable and soft to the touch for optimal performance that will last through wash after wash, retaining shape, comfort and protection levels throughout the life of the garments.
Getting more information on the Snickers Workwear clothing range is easy. You can call the Helpline on 01484 854788; check out www.snickersworkwear. co.uk and download a digital catalogue or email sales@hultaforsgroup.co.uk
Spacers? Pillars? They're not interesting at all are they? They're not sexy like iPhones, EVs or AI systems. No, they are not. But they are probably in smart mobile devices such as Alexas and Teslas. And if you go looking through the catalogue of a spacers or pillars supplier you'll find a huge selection to choose from. Why is that? Surely a couple of different styles in various lengths would do?
Pillars and spacers have only two functions to fulfil: they are designed to keep component parts such as PCBs and enclosures apart, and also to provide mechanical rigidity. Perhaps for this reason they are mostly overlooked by design engineers. But, consider this: a poor choice in spacer selection may make it very difficult for the production engineer when it comes to final assembly. If the assembly process
Let's first look at the basic shape of the pillar. Rounded, tubular models can look very attractive. But they can be difficult to grip, especially when using a jig or fixture in final assembly, and clamps may leave an impact on the round surface (Figure 1). Hexagonal designs, on the other hand, have less aesthetic appeal but may be easier to handle and assemble (Figure 2).
Then there is the question of the screw threadsome are threaded, some are not. The choice of which to use is a pure Design For Manufacture (DFM) challenge. How much space is there in the enclosure? Can the spacer be reached from the top and under-side, or just the top. Is it possible to access the spacer with a screwdriver? Or maybe an Allen key would be a better option?
What should we think about if the design calls for PCB stacking? It may seem simple to have one long screw and use multiple non-threaded spacers in between. But that may be tricky to assemble on a production line and tolerancing may become an issue. Instead, how about evaluating a stud design (Figure 3). Using such
issue, but still one which needs addressing. Plastic is lightweight and may be cheaper. But metal spacers will provide more stability and will not degrade due to temperature or direct light. Neither will they suffer from out-gassing which can be a major concern with space missions carrying sensitive analytical optical equipment. Plastic spacers are also more easily damaged by an operator who is heavy-handed with the torque wrench on the shop floor. However, they may be cheaper, and have unique shapes and features as discussed in a later paragraph.
connectors, and resulting in product failure.
So we may need more than one spacer on each corner. And we need to ensure that there is
spacer design that comes in a range of lengths and which simply pushes into place - no need for any further tooling operations. Simple, quick, effective.
Finally, let's go back and consider an essential function of the spacer: to separate PCBs and enclosure fixings. If the design doesn't pay enough attention to the number of spacers required and the placement, large PCBs could flex due to the weight of the components on the board and possible shock and vibration issues during product operation. If the design has not recognised this potential problem, adjacent PCBs could bow causing the components to crash into each other, damage board to board
Here's a question for all design engineers: why do you think that distributor Powell Electronics has just put in a stocking profile consisting of 63 different pillar/spacer part numbers from the manufacturer, Harwin? So that design engineers have multiple methods to choose the right spacer to make their production engineers happy.
For more information, see below. www.powell-electronics.eu
On the 28 – 29th March 2023, the NEC in Birmingham will welcome the UK’s largest IntraLogistics exhibition.
The Show is going to be packed and is set to welcome over 4000 visitors and over 250 exhibitors who will be showcasing their cutting-edge solutions and sharing secrets to their success. There will be live demonstrations across the two days and over 40 conference sessions offering practical insight on technological innovations.
IntraLogisteX is a completely FREE event to attend and will be packed with everything practitioners need to improve productivity, safety, maximise space and cut costs. Discover the latest in Storage, Warehouse Automation, Warehouse Infrastructure & Services, Robotics, IT & Software, Materials Handling, Packaging, and Picking & Sortation.
The event is designed for end-user practitioner logistics professionals such as warehouse managers, heads of distribution, IT directors and lead project managers, as well as logistics professionals who are looking for solutions to their current and future challenges, from the latest materials handling technologies to full-scale warehouse automation options.
Don’t miss out on the chance to liase and connect with some top brands such Brother, Diamond Phoenix Automation, EPG, Element Logic, Orion, Palband, and many more.
Book your tickets now.
www.intralogistex.co.uk
The Autotote is the next development in intralogistics containers. It is perfectly designed to offer smooth silent running, with its single shot double skin strengthen base and cantilever edges.
The innovation of the Autotote’s double skin concaved base is designed to run smoothly and quietly along automation systems, while maintaining a high level of durability and ultimate strength. The diagonal ribbing strengthens the base to the highest standard and the 100% closed underside protects the conveyor system, helping to save cost on belt maintenance, while improving grip and speed.
The base consists of a cantilever edge that reduces noise on rollers and a chamfered side edge that provides a smoother transition between linking conveyors or during a directional change. The Autotote also has several strengthened interaction points to optimise movement within an automated shuttle system
Intralogistics and automation warehousing is becoming increasingly popular throughout the globe and is pushing businesses towards future proofing their supply chains. The Autotote advances all aspects of the supply chain from improving accuracy and speed, to reducing waste, and is suitable for all conveyors and transfer units, with an optimised base design that reduces deflection and noise.
Dividers can be added to the Autotote for versatile subdivisions, allowing up to 1/8 segregation for increased fill and SKUs available per system. Other various optional extras are available and can help
modify the Autotote dependant on the specific needs of the company, including; easy recycle lift lid, automated barcode and label application, and both open or closed handle options.
Loadhog can manufacture the container with a blend of recycled and virgin material, helping you to protect your supply chain’s carbon rating. A circular economy is now globally recognise and promotion of this within your supply chain will not only future proof your business but ensure a long life investment.
As the importance of automation continues to grow, Loadhog’s new innovation is set to improve and modernise operations processes across a range of sectors. The global intralogistics market is expected to grow at an annual rate of 15.5% from 2020 to 2030, encouraging businesses to migrate from manual to automated warehousing and invest in the most reliable and efficient totes for a smooth process.
By
t
Zebra
Returnable
t Prevent asset loss or theft
t Improve accountability for customer disputes
t Reduce inventory counts from days to minutes
t Monitor asset lifecycles
Alex Whiting, Managing Director at MiTEQ, says “there are plenty of MiTEQ customers looking to accelerate their materials handling processes using automation and tracking solutions. Some
As your business grows and evolves, it’s important to have a packaging partner that can adapt and support your changing needs. That’s where Hazel 4D comes in.
We offer a wide range of packaging solutions and services to help your business succeed. Whether you’re in need of custom packaging designs, storage and inventory management, or nationwide distribution, we’ve got you covered.
Hazel 4D is more than just a packaging supplier - we are a true partner, dedicated to helping your business thrive.
Lowpad is a high-growth technology provider which arranges automation solutions for intralogistics based on intelligent autonomous mobile robots, intuitive software, custom-made vision, and handling applications. As experts in robotics technology, we are committed to engineering solutions that meet today’s evolving complex demands.
Improving operational excellence
At Lowpad, we aim to accelerate productivity and enable independence for organizations through safe, high-quality intralogistics solutions. We offer solutions applicable to existing load carriers, processes, and buildings, enabling
We were the first to launch Total Packaging Management, a solution that scales and flexes with your business. You receive your packaging on time and only in the volumes you need to meet demand. As demand increases or decreases, stock deliveries automatically follow.
Most importantly, you only pay for what you use, when you use it. This gives you the security of no longer worrying about stock outages without the added cost implications of increased stock holding.
As your packaging partner we adapt to
cost-effective and flexible technology for (food) retail, 3PL, Post and Parcel, horticulture, and e-commerce.
Automate your marshalling process
Take your marshalling to a new level, like DHL and GXO. Embrace flexibility,
support your changing needs and help you focus on the things that will drive your business forwards. It’s at the forefront of our 4th Dimension approach.
Want to learn more? Come visit our stand at IntralogisteX, Stand number: i700
For more information call +44 (0) 113 242 6999 or email wecare@hazel4d.com
speed, accuracy, and safety and reduce deployment of hard-to-find personnel and related costs. We offer a fully automated process where Lowpads moves your load carriers to the outbound area just before they are needed to be shipped.
Join Lowpad at Intralogistex
Get to know Lowpad. We’re exhibiting at IntraLogisteX. Visit stand i200 for a live demonstration!
Contact details Van Beukelaarweg 1, 2971 VL Bleskensgraaf, The Netherlands +31 184691107 sales@lowpad.com
for a huge
of
of 25
of 100kg on the belt at any given
01536 206600 sales@maceindustries.co.uk. www.maceindustries.co.uk
are looking to optimise already very complex systems, others are using basic scanning and computing technologies but want to take their efficiencies to the next level.”
RFID is one of many tools in the RTLS solution arsenal. The benefits of RTLS solutions overall include:
t Improved data accuracy and availability
t Digitised asset tracking and inventory management
t Time and money savings through automation
t Greater compliance, health and safety regulation
t Enhanced visibility and control of production processes
t End-to-end asset traceability (and quality assurance)
t increased revenues
If you are interested in solutions to accelerate materials handling processes for your business, MiTEQ will be situated on Stand i1120 at IntralogisteX.
taking place at the NEC on 28th and 29th March.
Visitors to the show can find Springpack at stand 310, where they will be showcasing their innovative and sustainable packaging solutions that help companies reduce their environmental footprint. With a focus on sustainability and reducing packaging waste, Springpack offers a range of packaging options made from recycled materials and biodegradable plastics.
“At Springpack, we are passionate about finding sustainable packaging solutions
that meet the needs of businesses while also protecting the environment,” said James York, Managing Director of Springpack. “We’re excited to have the opportunity to showcase our products and services at Intralogistex, and to share our vision for a more sustainable future.”
Attendees at Intralogistex will have the opportunity to see first-hand the wide range of eco-friendly packaging solutions that Springpack has to offer,
including their newly launch high performance, multi layered nano machine film – Armour Wrap. With a team of packaging experts on hand to answer questions and provide information, visitors to the stand are sure to leave with a better understanding of how Springpack can help them achieve both their sustainability goals and packaging requirements.
Don’t miss this opportunity to see the latest in eco-friendly and cost saving packaging solutions at Intralogistex. Springpack can be found at stand 310, and the show runs from 28th to 29th March. For more information, call 01905 457 000 or visit www. springpack.co.uk.
Dfor building and running an application. D:PLOY automatically discovers most of the installed hardware, and generates the robot motion based on the obstacles and cell boundaries defined in the workspace. The program logic, signals exchange, event handling, and robot movement are automatically created for the entire application based on a few inputs such as workpiece attributes and pick position.
D:PLOY offers unrivalled reduction in robotic cell deployment time and complexity. For example, initial deployment of a palletising application drops from 40 hours to 4 hours, for a 90% time savings. Just as critically, when production requirements
change, D:PLOY gives the flexibility to quickly re-deploy the application for new products or workpieces. Real-time monitoring improves productivity and minimises downtime.
About OnRobot OnRobot A/S was founded in 2018 with the mission of breaking down automation barriers and bringing the benefits of automation to manufacturers of all sizes. Headquartered in Odense, Denmark, with offices spread across the globe, OnRobot is the world’s leading provider of the broadest range of tools and application solutions for collaborative applications. All offerings are based on the same ‘One System, Zero Complexity’
philosophy, delivering a unified interfacing experience. OnRobot products and solutions are provided through more than 700 distribution and system integration partners and used in many different industries, making it easier and faster to automate tasks such as material handling, machine tending, assembly, and surface finishing.
Contact: Vikram Kumar, OnRobot GM for North Europe, UK and Ireland Vikram.kumar@onrobot.com www.onrobot.com
brand – all based on our ‘One System, Zero Complexity’ philosophy. Now that the building blocks are in place, we can finally launch the first version of D:PLOY, which will be a market enabler across the industry.”
D:PLOY addresses one of the industry’s greatest challenges: the shortage of skilled robotics engineers and integrators who can help smaller, less-experienced manufacturers break through existing barriers to automation.
Simon Potzkai, Robotics Sales Engineer at Alexander Bürkle, an OnRobot system integrator and a D:PLOY beta tester, said, “D:PLOY simplifies the task of building and integrating a robotic cell with an innovative approach that doesn’t require any type of programming. With the current shortage of engineers, that’s a huge advantage for integrators. By making it easier and faster for us to deploy automation, we can serve more customers and help them more quickly realise the advantages of automation. That’s a win-win for everyone.”
As an automated platform that works with many leading robot brands and can be applied to a wide range of common applications, D:PLOY can help speed up robotic adoption within the large untapped segment of small & mid-sized enterprises.
Alan Vallis, Training and Development Manager at LG Motion Ltd, an OnRobot distributor, said, “D:PLOY will make automation accessible for companies who may be a bit reluctant, whether it is related to cost or in-house skills and competences. I think D:PLOY will demystify a lot of that.”
How D:PLOY works
D:PLOY automates many of the manual steps necessary today
wo heads are better than one – the advantages of the Biral back scatter head for precipitation classification.
Automatic visibility and present weather sensors normally use the forward scattering of infrared light to estimate visibility and classify precipitation. Sensors produced by Biral emit a cone of modulated near infrared (850 nm) from the transmitter head, which is scattered by particles in the air. The intensity of scattering is not the same in all directions, since this is strongly dependent on the shape, size and composition of the particle.
How it Works
Infrared light emitted by the transmitter that is scattered by 39-51° is detected by the forward scatter receiver. This is sufficient to estimate the visibility and aid the classification of precipitation type. The infrared light which is scattered by 107119° is detected by Biral’s unique back scatter receiver, which is used in addition to the forward scatter measurement to help discriminate between different types of precipitation, such as rain and snow.
A diagram of the scattering angles in relation to a Biral visibility and present weather sensor is shown in Figure 1
Present weather sensors which do not have a back scatter receiver usually discriminate between rain and snow using only the forward scatter signal from an individual hydrometeor (raindrop or snowflake),
often combined with air temperature.
Biral’s back scatter receiver provides more detailed independent data on the precipitation type compared with using forward scatter alone. Specifically, the sensor measures the ratio between the back and the forward scattered infrared. Snow has a much higher proportion of back scattered infrared compared to rain (figure 2), so the back scatter head is able to reliably differentiate between rain and snow
The crystalline structure of a snowflake provides multiple facets for scattering of optical and infrared light in all directions irrespective of wavelength, especially back towards the transmitter. This accounts for the main reason a human observer can differentiate between rain and snow – because snowflakes are white! The same applies to other frozen hydrometeors such as ice pellets and hail, where back scatter from trapped air bubbles make the particle appear opaque, with increased backscatter.
An example of the relative difference between forward and back scattered infrared for different individual hydrometeors is presented in figure 3. These measurements were taken as rain turned to ice pellets then snow as a thunderstorm passed over a Bristol-based sensor on 2 March 2016.
Classifications were based on human observation, with approximately three minutes between the different hydrometeor types. Air temperature remained above freezing throughout, at 6°C during the rainfall and ice pellets, and 5°C during the snowfall.
The back scatter receiver is unique to the Biral present weather sensors and provides reliable discrimination between rain and snow. This is demonstrated by reports of excellent snow detection and discrimination capability from our customers and field trials with trained meteorological observers.
Back scatter receivers form part of our SWS 200 and 250 series and VPF 730 and 750 series. The Biral VPF-750 represents our most advanced visibility and present weather sensor, with the addition of external temperature and relative humidity sensors to aid discrimination between fog and non-liquid particles which lower the visibility, such as smoke, wind-blown sand, and dust. An integrated freezing rain detector allows reporting of all forms of freezing precipitation, providing a comprehensive and reliable account of present weather for all environments.
For more information, see below:
www.biral.com
St. Louis, MO – Watlow®, a designer and manufacturer of complete industrial thermal systems, is pleased to announce that it has signed an agreement to acquire Eurotherm® from Schneider Electric, the global leader in the digital transformation of energy management and automation. The terms of the transaction were not disclosed.
Eurotherm is a premier global provider of temperature, power, and process control, measurement and data management equipment, systems, software, and services for global industrial markets. The company’s headquarters are in Worthing, UK, with core manufacturing operations in Lędziny, Poland, and headcount of about 650 people worldwide.
“Watlow is excited to invest in this innovative product portfolio and professional team,” said Rob Gilmore, Watlow’s CEO. “Combining Eurotherm’s complementary controls technologies with Watlow’s focus on thermal systems, our shared engineer-to-engineer sales models
and our focus on common markets will allow Watlow and Eurotherm to better serve all of our respective customers. We are impressed with Eurotherm’s heritage in the controls industry and strong reputation for innovation and quality, so we are looking forward to welcoming the Eurotherm team to Watlow.”
Gilmore continued, “Watlow is investing aggressively right now, including development of our operations in Europe and Asia to ensure we can support and respond to our customers wherever they need us. This acquisition will help us expand our presence in Europe and extend our electronics and controls capabilities globally.”
“We are very pleased to be joining the Watlow team,” said Chris Ashworth, Eurotherm’s Managing Director. “Watlow is a known leader in the industry, and I believe that combining our strengths will open new opportunities and create value for our customers.”
For more information, see below.
www.watlow.com
The
and FPYL-532-100T-SLM-C have an outstanding wide operating temperature range between -40°C to +60°C. They are offered with either 50mW or 100mW at 532nm in a very compact housing of just 110mm x 52mm x 52mm. The spectral linewidth
is <0.00001nm which complies to a coherence length of >9m. With a power stability of <1% and a noise of amplitude <0.25% they are perfectly suitable for applications like:
t Confocal Microscopy
t RAMAN Spectroscopy
t Particle Measurements
t DNA Sequency
t Flow Cytometry
t Digital Imaging
t Analytical Chemistry
sales@frlaserco.com
www.frlaserco.com
Recent months have highlighted again the issue some supply chains are having. It doesn’t matter where you’re operating, whether you’re in the UK, the US, or elsewhere, we all have global supply chains now, and that is where the disruptions are.
We know that getting the right gas safety tools and equipment when you need them is becoming increasingly challenging due to supply chain challenges. Crowcon is dedicated to providing safety, health, and environmental technologies to support organisations across multiple industries. We know that you shouldn’t have to wait to
Interface Force Measurement Solutions (Interface) is a UK company specialising in the supply and distribution of high-quality sensors and associated electronics and displays for a wide variety of industries. Working previously with clients such as Airbus, BAE Systems, and Formula One Teams, we spoke with Tony Rokins, Business Development & Pressure Mapping Specialist, who explained some of the companies well known products.
“Our product portfolio is applicable to many industries. For instance, we are well known for our high-quality pressure mapping systems that are used by many of our automotive and motorsport customers. Our sensors deliver highly accurate, repeatable measurements and many of our load cells are used by calibration houses as calibration reference devices. Our high-quality, yet competitively priced 3 and 6 axis load cells are used for many R&D, renewable energy and robotic applications.”
In terms of recent developments, Tony continued, “Being responsive to our customer’s needs and being able to offer a high-quality product with strong product knowledge at a competitive price with the best possible lead times is our number one priority. Last year we launched our range of G-Series Load Cells. The range comprises of miniature and small sensors for industrial applications, with capacities starting from
ensure you’re safe at work or ensuring your people are safe. That’s why we’re dedicated to having readily available products when you need them most.
With a wide range of portable and fixed gas detection solutions, we can help find the right detector for you, no matter your application or industry.
Personal CO monitors and flue gas analysers are also available at a reduced lead time for all HVAC engineers. Our lead time for portable detectors and flue gas or
just 4.5N Newton up to 200kN with metric threads. These are highperformance devices but aimed at more cost-conscious applications. This is a new market for us, but we have already had increasing interest. We also launched our brand-new e-commerce website on the 1st of April for the G-Series that showcases Interface load cells at competitive prices with all the convenience purchasing online offers,” stated Tony.
The new e-commerce website offers G-Series load cells on short lead times with next business day delivery for small quantities. Following its successful launch in 2021, it has become an increasingly popular product range for students, industrial engineers, OEMs and anyone requiring a small form force sensor offering accuracy, repeatability and Interface quality.
In the future, Interface is keen to continue its growth trajectory for 2022. Tony mentioned, “we are also working on new, wireless force and vibration sensors for remote monitoring in systems such as luggage carousels. One more area we are pushing for growth is with XSensor’s pressure mapping systems, particularly in the Hi-speed systems designed for high-speed impact or crash testing and tire foot-print research. These systems are capable of capturing data up to 2,500 frames per second. The tire sensor can be driven over at speeds of up to 140kph. I believe this is a unique capability we can bring to the industry.”
As the company looks to continue strengthening its position with its customers in its more traditional markets of aerospace, automotive, motorsport, Universities and alternative energy research, it will be attending some expos over the next 12 months and be readily on hand to discuss any questions you may have about force, torque, pressure mapping or pressure, level & temperature measurement. These expos include
combustion analysers is 7 working days. With fixed detectors available from 7 working days.
www.crowcon.com quotes@crowcon.com
Bringing the industry together once again, CHEMUK 2023 is set to return on the 10 – 11th May 2023 in Hall 1 at the NEC in Birmingham.
This year the show will be presenting over 400 specialist exhibitors and over 150 expert speakers that will be split between three major show zones: Chemical Industries Supply Chain; Chemical, Process & Plant Engineering; and NEW for 2023 CHEMLAB – Laboratory & Innovation.
Brand new this year, the CHEMLAB Show will showcase specialist laboratory chemicals and chemical equipment suppliers supporting Research & Development, Analysis, Process Design & Development, Scale-Up, and Quality Testing within the Chemical & Chemical Product Industries. CHEMLAB will invite laboratory
professionals from across the chemical industries involved in a number of sectors such as Formulation Development, Reaction Process Analysis, Regulatory / EHS support, and many more.
The Chemical, Process & Plant Engineering show zone will be dedicated to Process Engineering Technology, Plant Engineering Solutions, Control & Instrumentation, Asset Management, and many more. This zone will be a great chance to meet specialist suppliers of Process Engineering and Chemical Plant & Asset Technology and Services, and is supported by IChemE, GAMBICA, BPMA and BVAA.
CHEMUK 2023 will host a number of exhibitors from a broad range of industries including Logistics, Operations & Fulfilment, Digital & Automation, Business Services – Skills, HR, Finance,
Laboratory, R&D, Analytical Chemistry & Process Scale-up and many more.
Visitor registration is now open for CHEMUK 2023
www.chemicalukexpo.com
As part of Schoeller Allibert Group, our company is based in Romont, Switzerland, since 1968. The manufacturing site is well known for the production of Injection Moulded Plastic UN containers under the brand name ROPAC®.
The comprehensive range of ROPAC® pails are UN certified for the transportation of hazardous solid and liquid goods, but also provide superior protection for our clients’ high value contents and the environment.
Our innovative and focused range of Plastic UN Liquid Containers are available in 5, 10 and 20 litre sizes and our UN Solid range are available in a range of sizes from 3 litres up to 32 litres.
We are proud to be key suppliers into the Chemicals, Fine chemicals, Inks, Coatings, Lubricants, Food and Pharma industries and work hard to deliver worldclass packaging solutions and services to these exciting and dynamic sectors. Our sales team is available to support and advise our clients globally and our R&D team are experts in developing new and innovative solutions in partnership with our clients and their needs.
www.schoellerallibert.com/uk/
Sera are the right fit for compact polymer preparation
As a worldwide leader in dosing technology, sera Technology is a system provider of high-quality products and services for the dosing and feeding of chemicals and fluids. With 75 years of experience, sera Technology is renowned for its excellent customer service and leading German engineering, offering some of the most robust pumps available on the market.
The PolyLine from sera is a series of simple, flexible as well as economical and high-performance systems for preparing polymers. The systems are equipped with precise flow measurement for solution preparation and level measurement to ensure efficient and economical operation of the systems.
The PolyLine is available in three different variants, each for use with liquid, powder polymer or as a variant for both polymer forms and we are now welcoming the new, smaller version - The PolyLine Flow Compact. With a footprint of 120 by 80 centimeters, it fits exactly on a Euro pallet. This means that it is not only cheaper to transport but can also be placed more easily at the customer's site and finds its place in every room and every application.
Come and see us at Chem UK 2023 for the first look at the new design.
www.sera-web.com
The world’s leading global trade show dedicated solely to AD and BIOGAS is set to light up the NEC in Birmingham on the 29-30 March 2023.
Hosted by ADBA and the World Biogas Association, there is an expected 30% growth in attendance compared to last year’s record number of over 2600 visitors.
BIOGAS 2023 will be hosted across two days where there is also two free-of-charge sideevents running: The Farmer’s Breakfast and The Local Authorities Lunch.
The Farmer’s Breakfast is a meeting about anaerobic digestions for farmers, on-farm AD plant operators and stakeholders. It will be staged at the World Biogas Expo and Summit
on March 29th where a panel of experts will detail how farmers can integrate AD and biogas production into their processes.
The Local Authorities Lunch is a meeting on waste recycling for local councils, investors, anaerobic digestion plant operators and stakeholders. Held between 13:00 – 14:30 on the 29th March, it’s a great chance to hear experts explore how local authorities can capitalise on the opportunity to align waste and energy streams.
The Show is set to host a record number of industry speakers including Anna AlessiProject & Communications Manager, Bio renewables Development Centre, Charlotte Marcel - Technology Strategy Lead, ADBA / WBA, Chis Huhne - Chair, ADBA, and many more.
TECH has developed an innovative and sustainable pre-treatment technology to maximise organic recovery from different solid organic waste streams and optimise anaerobic digestion facilities.
The BIOMAK® is an autoclave system based on a continuous thermal hydrolysis process that produces a homogenised, hygienised and degraded biomass from the organic fraction of waste. The BIOMAK® is a front-end unit that can process up to 8t/h of different types of waste, from source segregated organics like food waste, to mixed municipal solid waste with high levels of contamination.
The BIOMAK® used as a pre-treatment in AD sites increases biogas production yields, increases the plants processing capacity, allows for the introduction of new materials into the AD such as compostable packaging and boosts the efficiency of mechanical separation equipment. The BIOMAK® enables an optimal removal of contaminants such as plastics, textiles and other inert
Wolf System is one of the leading tank suppliers in Europe, with offices in 19 European countries. The in-situ reinforced concrete tanks built by us are used for a multitude of scopes, like digesters, buffer tanks or storage tanks for biogas plants, water and wastewater treatment plants, firefighting water and many more.
With over 2000 concrete tanks built yearly, we have experience in almost every European country, including the UK and Ireland, where we successfully completed almost 350 tanks on over 130 different projects in the past years.
Our tanks can have diameters of up to 50 m with storage capacities going beyond 10.000 m³ and are built using our proprietary formwork system that needs no anchors through the wall, ensuring the highest possible tightness from the beginning. We can also include in our scope a variety of tank accessories, like thermal insulation, concrete protection foil, central columns, access doors and others.
materials, while minimising the loss of organics in the separation stages.
A BIOMAK® project offers a quick return on investment with a standard payback below 5 years and enables full compliance with new organic waste regulations and the Net Zero Strategy.
If you are interested in developing a project or learning more about the BIOMAK® solution reach out to l.stone@econward.com.
Visit us at Stand C407 at the World Biogas Expo on 29-30 March 2023 at NEC Birmingham, or contact us at:
+43 7615 3000
mail@wolf-construction.uk
www.wolf-construction.uk
With
equipped to support every sector across the UK and Europe with a family of trusted brands: Link51, Apex, Polypal UK, Polypal Europe, HiStore, LinkLockers, Probe and LinBins. Industry standards Working in warehousing can be hazardous if companies don’t follow the relevant rules and regulations. There are a number of industry-based accreditations which put safety at the heart of everything they do and Whittan is proud to say that our products and installation services meet the following accreditations and quality standards.
t British Safety Council is dedicated to making sure no-one is injured or made ill through their work. Members must follow strict codes of practice to develop better workplace practices and drive towards the highest health and safety standards.
t British Standards accreditation shows that goods and processes have been assessed against internally recognised
standards and operate to the highest levels of quality and service.
t Constructionline is a qualification that enables buyers to quickly find subcontractors and material suppliers that are pre-qualified to government standards.
t CHAS (The Contractors Health and Safety Assessment Scheme) demonstrates a company’s compliance with and sound management of current health and safety legislation.
t SafeContractor ensures compliance across the supply chain, by demonstrating that all current legislation and regulatory process are met, to ensure health and safety standards.
Meeting product standards
As a Full Manufacturing SEMA (Storage Equipment Manufacturer’s Association) Member our products are submitted to independent product assessments. This guarantees they have been designed by a structural engineer to meet SEMA Codes and that system rigidity is calculated to meet precise criteria under specified conditions.
In other words, the racking will live up to the job it has been designed to do - carry heavy loads - and once loaded the rack and its components will not distort. To put it simply, when you purchase our products, you are also buying reassurance.
Meeting aftersales standards
All racking follows a circular pattern – you purchase the equipment, it gets installed and then it gets used. It’s important to consider the total cost of ownership, if not followed correctly it
For a chance to see the latest innovations in the business, as well as talk to like-minded people and suppliers, apply for your tickets now.
www.biogastradeshow.com
Poor soil quality across the globe causes ever more growers to use organic and chemical fertilizers. Numerous studies have shown that organic fertilizers produce more and contribute to sustainable agriculture.
The current supply of natural gas and shortages on valuable resources like Potassium and Phosphor causes Fertilizers to reach record high prices. Besides, the production of chemical fertilizers, is one of the biggest emitters of Carbon Dioxide in to our atmosphere, contributing to global climate changes.
The need for organic fertilizers plus the carbon intensity and high prices of chemical fertilizers, require innovative solutions to upgrade waste-streams from Anaerobic Digestion plants in to valuable products. TEMA Process has developed a unique solution to turn various waste streams from AD-plants in to a granulated Fertilizer, using Fluidized bed technology. This product has a high organic fraction and a high concentration of Nitrogen, Potassium and Phosphor, making it an excellent fertilizer, produced from waste streams with a small carbon footprint and very economical.
P&M Pumps and Vaughan Company are returning to the World Biogas Expo after a short break. The unique Rotamix pumped tank mixing system will once again be the focus of attention with live demonstrations of the Chopper Pump (first patented chopper pump in the world going back to 1960) and a scaled down working demonstration of Rotamix.
Vaughan Co and P&M Pumps Limited celebrate a 30 year relationship this year with continued impetus in providing equipment that is reliable durable and efficient in maximising available working volume in digesters thus ensuring biogas production is maintained at an elevated level with enhanced equipment availability.
The unique dual zone mixing pattern from Rotamix nozzles placed in specific positions ensures a digester mixed with more than 95% available working volume by combining the areas of higher velocities seen with other mixing technology that usually causes deposition in either the centre of a digester or at the periphery, with unmatched process and guarantees and hardware.
The TEMA Process drying solutions distinguish themselves with the following unique features:
t Drying of a mixed stream of thick fraction and concentrated thin fraction into a granulated
t Fertilizer with the total use of heat from CHP including exhaust gases.
The World Biogas Expo stand C701
The Vaughan chopper pump, manufactured in the United States by Vaughan Company continues to be the pump of choice for many Waste water companies and AD operators where other so called ‘Chopper Pumps’ fail to produce.
Visit us at Stand D107 at the World Biogas Expo or contact Director, Andy Parr for more information:
andy@pumpmix.co.uk
www.pumpmix.co.uk
can rapidly accelerate the overall expenditure.
Your racking is classed as work equipment and under PUWER you must perform daily and weekly inspections by properly trained in-house employees. Do they provide training on how to conduct these inspections? You must also conduct a yearly ‘expert’ inspection by a qualified professional. Our SEMA Approved Racking Inspectors are skilled engineers who can assess
Efor smaller rooms such as utility rooms, ensuites or washrooms – for which you might also choose a fully tempered frameless glass door to allow in extra light and add a touch of elegance. ECLISSE sliding pocket door systems offer fantastic flexibility. They can be used to partition off a workstation or home office, creating a sense of division between workspace and personal space. They can be closed for intimate events, or opened up for parties. They offer convenient connections between rooms such as the dining room and the kitchen, or bedrooms and ensuite bathrooms.
Smooth Running and Robust Construction
ECLISSE sliding pocket door systems come complete with the runners and are sold with a 15-year guarantee. They are designed for maximum smoothness and fluid sliding movement of the door. They are reliable and robust and are suitable for use anywhere in the home including bathrooms and ensuites.
Showroom
Our fully functional showroom in Grantham offers architects, specifiers, housebuilders and homeowners the opportunity to see our products in action, in a real-world scenario. Our product
experts at ECLISSE UK will guide you around the showroom, explain how each system is designed and help you to decide which system is most appropriate for your requirements.
They will fully demonstrate the functionality of each system and the associated accessories such as the BIAS (Soft-Close with Built-In Anti-Slam) system, the Touch Latch, or self-closing systems, as well as explaining and demonstrating the benefits of each. We can also offer in person, in-situ advice on sizing and installation as well as providing literature to take away and links to our professionally produced instructional videos which make the process of installing our systems simple and quick. As our product experts show you around our showroom, they will demonstrate the internal workings and structural mechanics of each system as the back of every display is exposed. This combination of fully equipped showroom and one-to-one access to our product expert essentially gives you the chance to try before you buy, virtually ensuring you will be happy with your new sliding pocket door system for many years to come.
Customer Support ECLISSE offers UK-based customer support for purchasing and aftersales, plus technical and installation advice through our friendly Customer Services team of product specialists based in Grantham. See the website for full details on technical specifications and step-by-step videos of assembly and installation.
T 0333 5770828 info@eclisse.co.uk www.eclisse.co.uk
In this issue of Industry Update we are pleased to announce Winn & Coales (Denso) Ltd as our Corrosion Prevention and Sealing Technology Company of the Month.
Celebrating 140 years’ service to industry this year, Denso is a leading manufacturer and supplier of corrosion and chemical resistant coatings and linings for long-term effective protection of buried, submerged, or exposed steel and concrete pipes, tanks, and structures.
“As a business, we have been supplying corrosion prevention-specific solutions to our customers problems for the last 90 years. We are most famous for Denso™ Tape, our renowned multi-purpose, anticorrosion petrolatum tape. Denso™ Tape is extremely versatile, easy to use, surface tolerant and long-lasting. This is what makes it such a popular choice on a variety of application types across a broad range of industries,” stated Keith Corfield, UK Sales Manager.
The company is able to draw upon a wealth of experience in producing its well-known quality brands such as Denso™, Premier™, Archco™, Protal™, Premier
Shrink Sleeves™, Steelcoat™, SeaShield™ and Sylglas™; all of which are synonymous with quality. “We have gained an enviable reputation, both nationally and internationally, for providing high-quality, longlasting solutions to our customers problems. We are committed to providing unrivalled service to our customers and have the knowledge and experience (supported by accurate, reliable information and data) to confidently recommend the most suitable and effective solution for the job. This attention to detail coupled with our ability to tailor bespoke solutions to our customers problems, is what makes us stand apart from our competitors,” added Keith.
One notable product from the Denso™ range is the Denso P1 System™ to which Denso™ Tape is a key component of. The Denso P1 System is a CESWIcompliant system for the protection of ferrous pipes, joints, and fittings within the water industry. It comprises a coat of Denso Paste™ followed by the use of Denso™ Profiling Mastic to fill any pits or voids, and to form a smooth profile for wrapping any joints, flanges or couplings. The system is then completed with an application of a double layer of Denso™ Tape. The easy-to-apply system is produced in accordance with ‘Civil Engineering Specification for the Water Industry – 7th Edition’, can be cold-applied, and delivers effective, long-lasting protection when
following correct application procedures. Case studies of where this product has been used can be viewed on the website.
Over the last few years Denso have been implementing a programme of investment with updates to premises and manufacturing capabilities across the entire Winn & Coales International group of companies, in order to keep up with demand from its customers and to fuel continued growth. A major development from this occurred in 2021, when Denso welcomed the acquisition of the global Viscotaq™ business; the ultimate visco-elastic coating and sealant used for the protection of above and below ground substrates, across a broad range of sectors, from corrosion.
If you’re interested in trying these products but would like more guidance Denso also offer training for this.
“To ensure our customers receive the best out of our extensive range of products, we believe in educating them in correct product application techniques. We offer free training either on site or in our dedicated training centre at our Head Office in South London. It’s a great privilege to be recognised for the work that we do and comes at the start of a fantastic year celebrating 140 years of service to industry,” said Keith.
For more information, see below.
T 020 8670 7511
www.denso.net
Treston is not just a furniture manufacturer. We offer our customers comprehensive know-how and insights on how to make their workstations and workspaces as functional as possible.
Ergonomics is always taken into account when designing a workspace and because Treston products are modular, the workstation solutions we design are costeffective and comply with the principles of the LEAN philosophy. Our range of products with ESD protection and our expertise in ESD matters help our customers obtain safe and functional workspaces for the most demanding working conditions.
Our long history as a furniture manufacturer, more than 500,000 workstations delivered, and 15,000 customers globally are a guarantee that we know what we are doing.
In projects, our expert sales staff go through the customer’s needs, goals, current state, and processes. Based on the conversations, we then make design proposals for the spaces and furniture. Our design engineers can make the exact type of dimensional drawings that the customer needs.
Our retailers are also experts who can provide the services that you need flexibly and comprehensively. We also support our network of retailers through expert services.
At Treston, our wide selection of products and modular and adaptable workstation solutions ensures that our customers find furniture solutions to meet their individual needs cost-efficiently. Being a manufacturer enables us to flexibly create customised solutions.
Easy workspace design with the 3D Configurator
Designing an individual workstation is easy and quick with our 3D Configurator software, available at 3d.treston.com. The 3D Configurator guides you through the selection of all the necessary modules and accessories for your workstation.
When you have completed the design, you can send a request for a quote
electronically, or save the drawing and supply list in PDF format on your own computer with a click of a button. We also offer an assembly service.
There is a comprehensive network of installation services that we use regularly at Treston, and we can also recommend, especially for use in larger projects, to
speed up the implementation of changes to manufacturing facilities.
At Treston, our expert sales staff and network of retailers, our modular products, and our opportunity as a manufacturer with its own factory to form customised solutions, guarantee that we can create an efficient and functional workspace for our customers.
Do not hesitate to contact us if you are looking for a smart and functional solution for your working environment.
For more information, see below.
T +44 (0)1635 521521 salesuk@treston.com www.treston.com
Mould making isn’t easy. There are many intricate challenges that include: highly complex geometry with 2D and 3D features, managing a wide range of part sizes, and short lead times on small quantities and new designs with no room for error. Compounding these challenges is the pressure to keep up
with the rapid pace of demand and technology.
But there’s a way to overcome those obstacles: Do better work with technology designed specifically for complex mould making.
Our USC-M series Milling and Drilling
Centres allow you to drill faster and mill better with a single machine and fewer setups. These Milling and Drilling Centres meet the challenges of milling and gundrilling all types of metals with either a single universal combination spindle or dedicated milling and drilling spindles. Utilising high performance spindles that provide exceptional rigidity
and power transmission, these machines deliver high-torque milling capability for aggressive metal removal and shorter cycle times. Additionally, 5-axis positioning enables mould manufacturers to tackle complex geometries with exacting precision in a single setup.
Many manufacturers claim to provide milling and drilling in a single machine, but the truth is those hybrid machines neither mill nor drill well enough to make a significant difference in either operation. In effect, one process is an afterthought of the other. Our USC-M series, however, was designed from the beginning to be a single machine with superior milling and drilling performance and accuracy. State-ofthe-art milling technology is embedded into a machine that has the power, thrust, speed and process monitoring competitors thought would be difficult to attain, or simply not possible.
In addition to superior quality and accuracy, the pay-off for single setup milling and drilling is efficiency and an improved bottom line. Mould makers cut delivery times to their customers with faster setups and production along with reduced overall labor costs. Once they move away from mould making operations with two machines, most of our customers find they can’t afford to manufacture without a USCM-series Milling and Drilling Centre.
The benefits of milling better and drilling faster with USC-M series machines do not stop at the spindle. There are intangible benefits as well. UNISIG USC-M series Milling and Drilling Centres allow mould manufacturers to approach their work differently and explore different approaches to mould making. With the entire manufacturing process streamlined, customers find their engineers and design teams enjoy more freedom and flexibility with the expanded capabilities. Finishing and assembly are faster because the design is more efficient, and manufacturers can do things effortlessly that were a struggle previously.
Ultimately, it’s about setting the bar high and keeping it there. UNISIG sets a standard looked up to by the competition. It’s a state-of-the-art mindset that takes mould finishing to a new level with a machine that allows you to mill better and drill faster.
www.unisig.com
In this issue of Industry Update, we have selected Quantex as our Pump Technology Company of the Year.
We awarded Quantex our Company of the Month Award last year and they have continued to impress with exceptional fluid delivery solutions, sure firing its fixed, global position.
Quantex offers off-the-shelf, recyclable pumps with additional varying flow-rate ranges. In 2021, Quantex was acquired by PSG, an operating company of Dover Corporation and now sits alongside 13 other pump and flow measurement brands. We caught up with Director of Marketing, Gillian Harding-Moore to find out more about last year,
“We’ve had an exceptional year, full of change. Benefiting from a ‘one company’, collaborative culture, we’ve been integrating with sister brands in Germany, laying the foundations for rapid growth in 2023 and beyond.
Perhaps the biggest change is the move of our Head Office to Duisburg in Germany, joining our PSG sister brands: Quattroflow, Almatec and Hydro, making future collaboration even easier. At this established and quality-assured facility, we have more resources and manufacturing facilities, including 380msq of ISO 7 certified clean room facilities.”
Quantex’s London office and dedicated manufacturing plant in High Wycombe remains fully operational and with a further rebranding of the high-quality pumps, Quantex has harnessed the power of visible readability for customers. The pumps have been renamed to match corresponding maximum flowrates, allowing customers to select the right pump quickly and accurately.
This leading company has doubled pump production since 2021, through increased manufacturing, showing
this company’s eager prowess in the industry. With a further automated assembly line planned for the Bagin-Box pumps, it is expected that the pump production capability will triple this year.
Quantex is a very worthy recipient of our Company of the Year Award, with exciting purposeful rebranding, exponential manufacturing figures, an incredible 100% growth in turnover during 2022, with its harmonious collaborative culture.
Quantex is the cutting-edge provider of recyclable pump technology, instead of the pump being attached to static equipment, it is uniquely fastened to liquid packaging, as part of a fully integrated fluid packaging system.
The pump is clipped into a motor drive, allowing the liquid to be dispensed at different flow rates, dependent on the liquid. Once the liquid supply is depleted, the customer replaces the bag with a corresponding new bag and pump, as Gillian illustrates,
“Quantex Pumps carry an exceptionally hygienic solution, especially with possible aseptic and sterile versions of the pumps, meaning that cleaning is eliminated since no product travels through the fixed machine. In addition, multiple products can be swapped in and out of the same channels with no cross-contamination.
Further advantages include: pump maintenance/ calibration are eliminated due to Pumps being replaced
with product packaging and the cost and footprint of the dispensing equipment is greatly reduced – due to the simplicity and wide availability of the mechanics required to drive the pump.
Furthermore, high vacuum capability means selfpriming, better bag evacuation/less waste, and highly viscous fluids can be pumped successfully. Usability is increased by the reverse cycling of the pumps allowing the dispenser to suck the product back in to eliminate drips and provide a clean dispense.
Ultimately, if brands can create higher concentrations of their products, our dilution pumps will enable them to take water out of the distribution channel, saving shipping costs and carbon emissions.”
Sustainability and cost-cutting are current priorities for many companies around the world and Quantex pumps help reduce expensive, rising shipping costs, offsetting carbon emissions by transporting less water, herby minimising product shelf-space requirements.
Quantex has been busy refining these existing, excellent pumps even further, as Gillian explains,
“We have a number of exciting new products in the pipeline for 2023, including our new High-Speed Eco Pumps. These use air pressure to activate the diaphragm and seal the pumps instead of a silicone spring, so they are more easily recycled, and can run almost three times as fast as our standard or high-pressure pumps. We are also working on new, easy-to-use Evaluation kits and pump driver technology which is primarily designed to help our OEM customers evaluate and integrate our pumps into their equipment more swiftly.”
The Quantex team had a successful run last year showcasing its unique recyclable pump technology at The Packaging Innovations & Empack at the NEC last May. The team exhibited two of its most popular dispensing machines in beverages and retail refill: Fresh Blends® Frozen Beverages Self-Serve IoT Platform and FillX’s Supershelf™.
There was a flurry of interest in both products from interested trade delegates. The ‘Supershelf™’ is a stateof-the-art new dispenser, allowing retail customers to sustainably refill existing bottles from bulk containers, making unnecessary existing, packaged containers redundant. Single-use packaging is one of the biggest villains of the plastic waste industry and this innovative product is helping end endless landfill waste.
The future looks bright for Quantex with exciting progressive projects planned as Gillian demonstrates,
“In the near future, we’ve got some exciting collaborative projects planned with our sister PSG brands in multiple sectors including Biopharma, Industrial Cleaning and Agriculture.
Over the next few years, Quantex will be supporting its Refill OEM customers to develop and establish an optimal, standardised platform for retailers, combining a delightful user-experience with IoT technology, with streamlined supply chain and shop-floor maintenance.
We will be growing our Industrial applications, where our pumps are used to reduce downtime for cleaning and maintenance in manufacturing lines.
Our technology is entering the Biopharma sector, offering hygienic and low-shear micro-dosing capabilities for cell and gene therapy and low-flow upstream applications. It’s an exciting sector where our pumps can make a difference.”
Quantex has unreservedly demonstrated a commitment to not only continuously producing quality-assured pump technology but by fully embracing the technological age, it has once again contributed to leading sustainable, ecological products.
At Industry Update, we love to award innovative companies and Gillian was honoured to receive this award on behalf of everyone at Quantex,
“We’re delighted – it’s an honour to be selected alongside many other established brands. Industry Update is a renowned publication and we’re proud that this award will help spread awareness of Quantex and the capabilities of our pumps.”
For more information, please see below.
T +49 (2065) 89205-0
www.quantex-arc.com